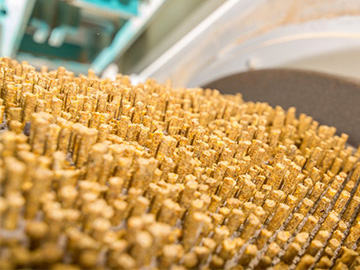
How To Maintain The Feed Machine Machine?
In the process of pellet feed production, if the user does not operate the feed pellet machine correctly, it will undoubtedly affect the service life of the feed pellet machine. How can we better reduce the wear of vulnerable parts of the feed pellet machine? Let's share with you the wear cause analysis and maintenance methods of vulnerable parts of the feed pellet machine.
Make a Quick Inquiry Now !1. Raw material particle size
Because the crushing fineness of raw materials determines the surface area of pellet feed composition, the finer the particle size is, the larger the surface area is, the faster the material absorbs water in steam, and it is relatively easy to condition and particle forming; If the grain is too coarse, the die wear increases, the energy consumption increases, and the productivity decreases.
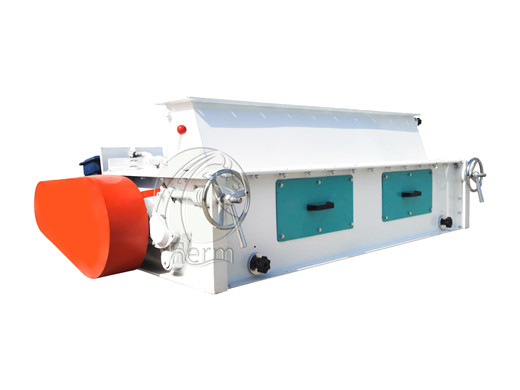
The requirements of animal feed equipment manufacturers are that the particle size of raw materials after crushing shall all pass through the 8-mesh screen, but the material on the 25-mesh screen shall not be greater than 35%. For materials with high crude fiber content, a certain amount of grease shall be added in the granulation process to reduce the friction between the material and the ring mold, and the appearance of formed feed particles shall be smooth.
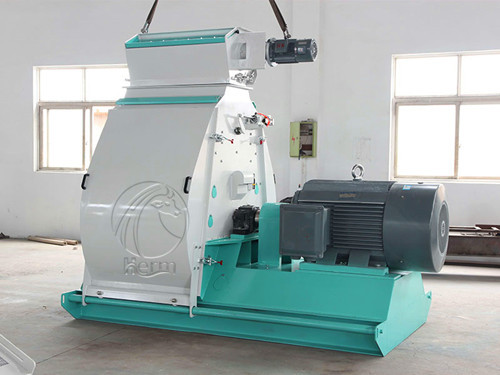
2. Raw material impurity cleaning
If there are too many iron impurities in the material, resulting in accelerated die wear, this should attract the attention of the pellet feed-making machine operator. Therefore, impurity removal before raw material processing is very important.
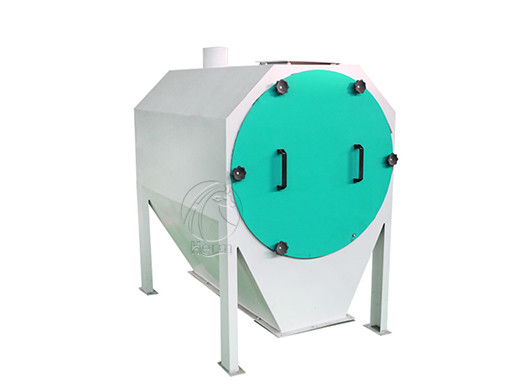
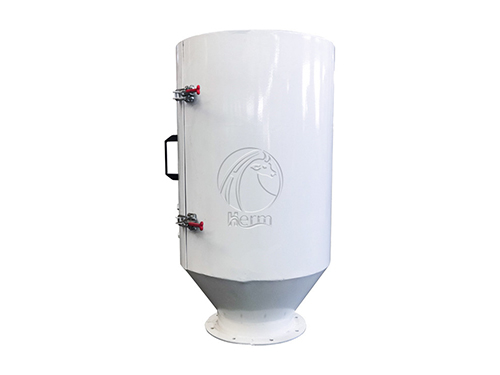
3. Add steam
Adding steam during material granulation is conducive to material softening and lubrication, to reduce the wear of materials on the machine and improve the output. Generally, the pressure varies with the variety of pressed materials. After adding steam, the moisture content of materials should reach 16% ~ 17%, and the temperature of materials after quenching and tempering should be controlled at 78 ~ 87 ℃.
4. Clearance between ring die and press roll
The unreasonable installation angle of the feeder will lead to uneven material distribution between the ring die and the press roll, and over time, it will lead to uneven wear distribution between the ring die and the press roll.
The gap is too small, which aggravates the wear of the surface of the ring die and the press roll, especially during the animal feed pellet machine running when the equipment is started and stopped. The gap between the ring die and the press roll is preferably 0.2 ~ 0.4mm, and the small value is taken when pressing a small-diameter feed or replacing a new ring die.
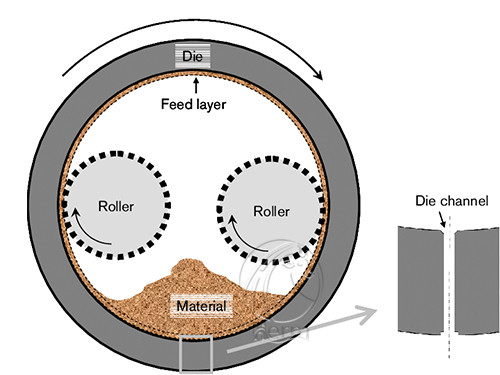
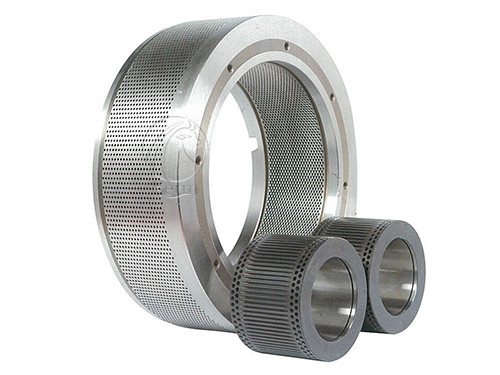
How to do routine maintenance?
Minor maintenance: once every six months, including the following contents:
1. Check and adjust the clearance of the main shaft bearing, and the radial runout of the hollow shaft head shall not exceed 0.05mm.
2. Disassemble and wash the feeder and modulator bearings and replace the lubricating oil.
3. Check the wear of the modulator blade and replace the damaged part.
4. Check and replace the damaged cutter.
5. Repair and clean the pressure-reducing valve, filter, drain valve, steam separator, valve, etc. of the steam system.
6. Disassemble and wash the pneumatic triplet and solenoid valve.
7. Check whether the bolts in the motor junction box are loose and replace the damaged sealing ring of the junction box.
8. Check whether the anchor bolts are loose.
9. Add oil to the pulley of moving parts such as the cutter moving device, door handle, and hinge lifting device.
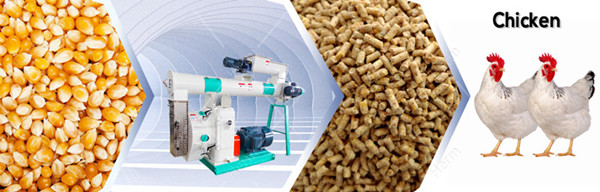
Medium maintenance: once a year, including the following contents:
1. All contents of minor maintenance.
2. Check the service condition of the motor bearing and replace the grease.
3. Check the use of the shifting knife and replace it in time if it is seriously worn.
4. Replace the V-belt with serious wear and reduced elasticity.
5. Check and clean the condensate on the oil circuit of the main shaft and pressure roller shaft.
6. Adjust the clearance of the main shaft bearing of the chicken feed machine.
7. Calibrate ammeter, voltmeter, thermometer and tachometer.
8. Check relevant lines and electrical components and replace and repair them in time.
9. Replace the damaged press roller spring washer box sealing ring.
10. Check the wear of the pulley and the reliability of the key connection.
11. Check whether the safety device is flexible and replace the failed parts.
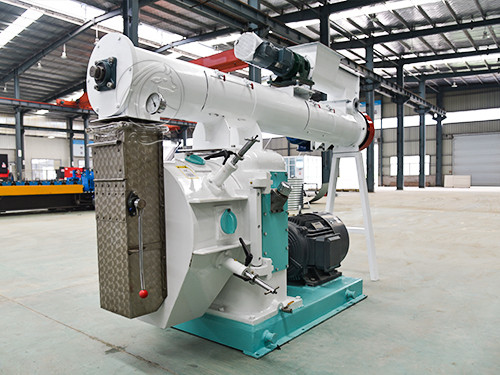
Major maintenance: once every 2 years, including the following contents:
1. All contents of maintenance.
2. Check the operation of the main shaft bearing and replace the seriously worn or damaged bearing.
3. Check the wear condition of the spindle, modulator, and spindle head, and repair or replace it in time if it is serious.
4. Check the wear condition of the wear ring and the keyway on the frisbee. If it is serious, repair or replace it in time.
5. Replace the severely worn copper sleeve of the main shaft.
6. Replace the deformed main shaft oil seal.
7. Derusting and painting of feed pellet machine body, pipeline, and support.
Henan Herm Machinery Co., Ltd was established in 2010 and has been devoted to the research and development of Feed Mill Machinery ever since. With more than 10 years of experience, Herm® has become a leading manufacturer and supplier of animal feed machines and complete animal feed production lines, cattle feed plants, poultry feed plants, animal feed pellet production lines, etc. It always endeavored to improve the quality of products and aims to meet the new requirements of the international market.
If You Are Ready to Start a Feed Pellet Plant Business, please contact us for the feed mill machine. We Can Provide Professional Design and Comprehensive Guidance According to Your Needs. Get in touch with us now!
Welcome Contact Us!
Henan Herm Machinery Co., Ltd
Email: info@hermmachinery.com
Whatsapp: 0086 18037508651